1. Project Background
A main municipal road had experienced frequent issues such as structural subsidence and expanding cracks in recent years. Conventional detection methods struggled to accurately identify deep-seated defects, posing risks to road safety. The municipal management department decided to adopt 3D array radar technology to conduct a systematic "health check" on a 2-kilometer-long critical segment. The goal was to efficiently identify underground cavities, pipeline misalignments and structural layer anomalies, providing scientific support for subsequent repairs.
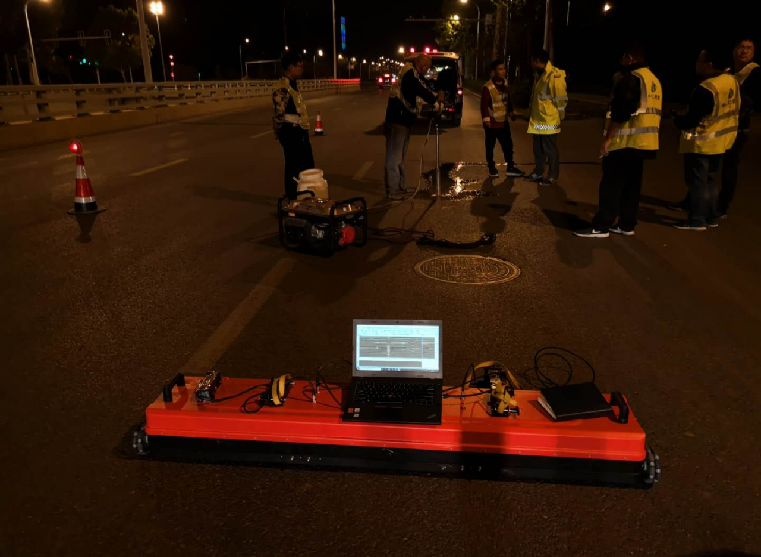
2. Detection Plan
Equipment Selection:
The LGPR 3D Array Radar System (Model: LGPR 3D-400AT10) was selected for its advantages:
o High Resolution: Central frequency of 400MHz, capable of penetrating up to 2 meters below the road surface.
o Multi-Channel Synchronization: 10 channels spaced 14cm apart, ensuring full coverage without blind spots.
o High Efficiency: Detection speed ≥20 km/h, enabling 5–8 km of road inspection per day, significantly shortening the project duration.
Survey Line Planning:
Detection lines were deployed along both directions of the road, focusing on areas with severe rutting, manhole covers, and historical subsidence points. GPS coordinates were recorded at the same time for precise subsequent location identification.
3. Inspection Process
On-Site Deployment:
The array radar system was mounted on the rear of a detection vehicle, adhering closely to the road surface via magnetic fixtures, to collect electromagnetic wave reflection signals in real-time. Technicians adjusted signal gain and filtering parameters in real time to ensure data stability under complex road conditions.
Dynamic Detection:
The vehicle moved at a constant speed 15–20 km/h, with the radar collecting 200 data sets per second to generate continuous 3D geological profiles. Multiple signal anomalies were identified, characterized by sudden changes in electromagnetic wave reflection intensity or distorted waveforms, indicating potential defects.
Challenges and Solutions:
Traffic Interference: Operations are conducted during low-traffic periods at night to reduce the impact of vehicle vibrations on data quality.
Pipeline Interference: Municipal pipeline drawings were cross-referenced to distinguish existing pipeline signals from abnormal reflections, reducing mis-judgement rate.
4. Detection Results and Verification
Typical Defects Analysis:
Deep Cavity (Depth: 70cm):
Located beneath a right-turn lane at an intersection, the radar profile showed a distinct "inverted bell-shaped" anomaly area (Figure 1). After drilling verification, the cavity has a diameter of approximately 1.2 meters, filled with loose sand and mud, posing a collapse risk.

75m (Figure 1)
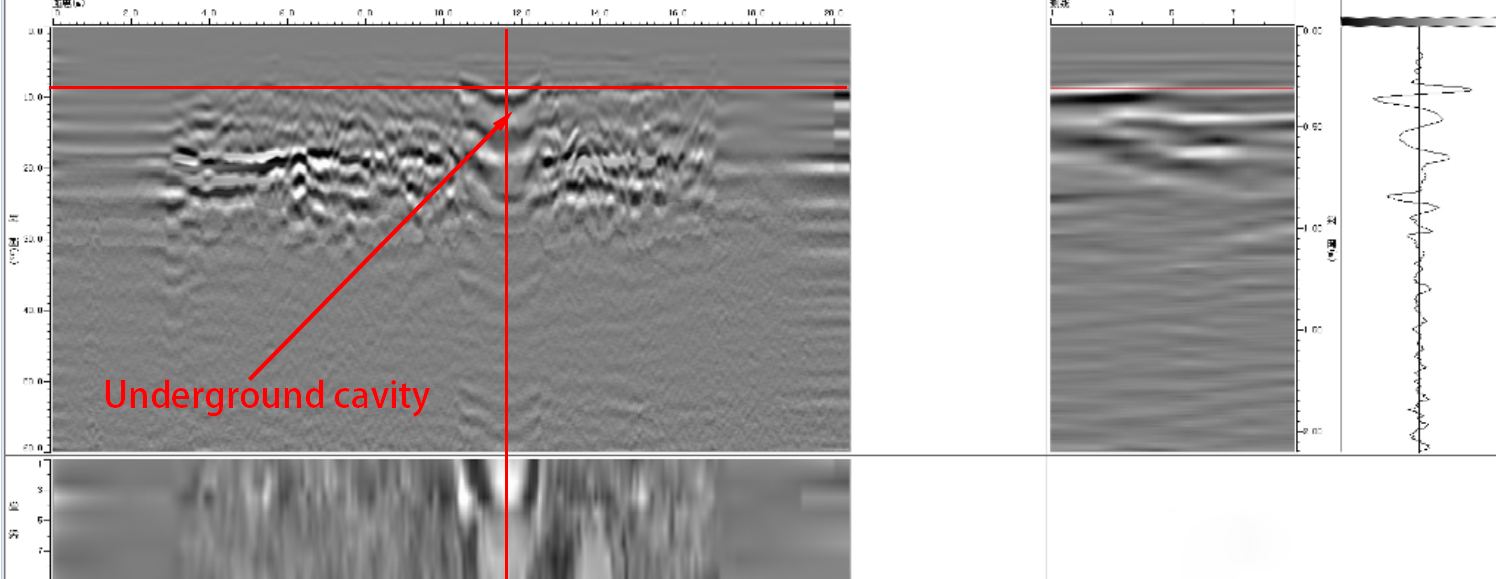
(Figure 2)
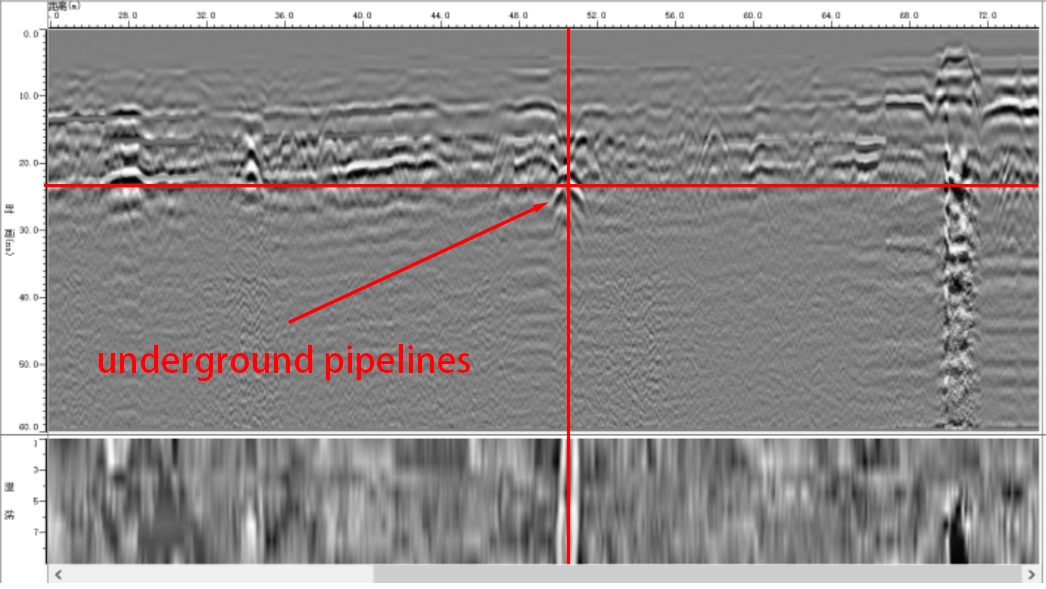
(Figure 3)
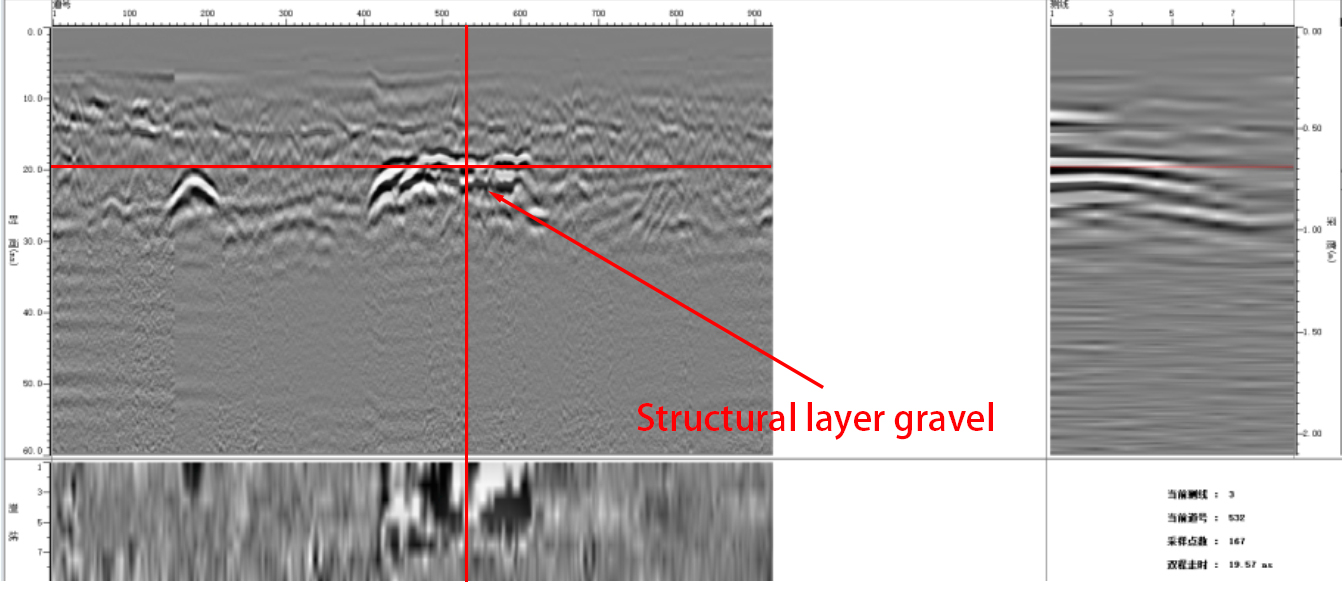
(Figure 4)